< List of Award-Winning Companies in FY2024 >
2024 Examination Results
As a result of examining the excellent efforts for product safety by companies and organizations that applied in FY2024, 18 companies have earned awards.
Click here for the list of FY2024 judges
Manufacturers and Importers Category
Category | Winner |
---|---|
Major Company Manufacturers and Importers Category
|
|
Small and Medium-Sized Companies Manufacturers and Importers Category
|
|
Retailer Category
Category | Winner |
---|---|
Small and Medium-Sized Companies Manufacturers and Importers Category
|
|
Special Award
Category | Winner |
---|---|
Businesses Category
|
|
Online Marketplaces Category
|
|
Manufacturers and Importers Category
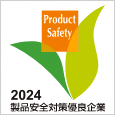
Established | 1949 |
---|---|
Representative | Director, Representative Executive Officer, President, and CEO: Kinya Seto |
Number of employees | 49,310 (As of March 2023) |
Location: | Shinagawa, Tokyo |
Business | Manufacture and sale of construction materials and installation equipment for residential housing and buildings, other businesses incidental to housing, and related services |
URL | https://www.lixil.co.jp/ [external link] |
Reason for Winning
●Optimizing construction and accident prevention initiatives through DX promotion
Active promotion of DX with regards to construction to prevent accidents that result from poorly executed procedures. This includes the launch of the “LIXIL-X” website for technicians to view the operation procedures at all times, as well as the adoption of the “Furosupport Navi” app that records traceability in the construction process and judges the quality of fixed joints by way of pictures taken on the site on smartphones.
●Utilizing CAE analysis to design and develop safer products
By utilizing CAE(Computer Aided Engineering)analysis, they can examine the musculoskeletal loads experienced by the elderly when using our products and the rising temperature of externally-installed metallic components in the artificial wood decking materials due to climate change. As such, they are able to discover previously unknown hazards, which leads to the design and development of safer products.
●Further growth from last year’s award
After winning the Excellence Award last year, they have continued to improve their product safety initiatives through determination and hard work. This includes establishing a unified product safety standard across all their companies under the Safety and Quality Management Division at headquarters, as well as providing educational classes to elementary and middle school students, and enriching the educational content through industry-academia collaboration.
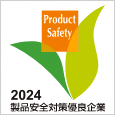
Established | 1954 |
---|---|
Representative | President, and Chief Operating Officer (COO) |
Number of employees | 383(As of March 2024) |
Location | Chiyoda, Tokyo |
Business | Domestic sales and import/export of razors, nail clippers, kitchen knives, cooking utensils, confectionery tools, cosmetic accessories, etc. |
URL | https://www.kai-group.com/ [external link] |
Reason for Winning
●Utilizing text mining tools to analyze and improve the voices of the customer (VOC)
The voices of our customers (VOC) regarding their products, such as company inquiries and uploads to social media, will be gathered and managed in their centralized in-house database. From there, they utilize text mining tools to filter out meaningful critiques and information pertaining to safety, which they can use for various product safety measures, such as in design development or discussions related to product recall.
●Collecting information about product accidents from Japan and overseas and its application in design development
They continuously collect a wide range of accident information pertaining to all kinds of consumer products in addition to their own, from Japan to the USA, Europe, Australia, Canada, and China. In addition to root cause analysis, they also share this information through in-house meetings and systems. Any knowledge gained, regardless of whether it pertains to a bladed product or not, will be utilized in the development of a product that they have never handled before in their electrical cooking utensil lineup.
●Building a culture of product safety through the certification system for becoming a Meister
The purpose of every employee is to be able to “talk about and explain bladed products in detail.” For this, they have installed the “Meister System” to encourage employees to learn about proper ways to handle products, including sharpening skills. Qualified and certified individuals are then tasked with holding seminars for wholesale stores and piquing consumer interests at storefronts, in addition to building a culture of product safety.
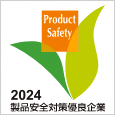
Established | 1918 |
---|---|
Representative | Representative Director and President Executive Officer |
Number of employees | 1,314(consolidated)(As of November 2023) |
Location | Osaka, Osaka |
Business | Manufacturing and sales of kitchen appliances, home appliances, and living products, as well as related businesses. |
URL | https://www.zojirushi.co.jp/ [external link] |
Reason for Winning
●Pioneering safety standards that are ahead of our competition and elevating industry standards
In light of scalding accidents caused by overturned electrical water boiler products such as electric kettles due to the carelessness of users, they formulated their very own testing and requirement criteria to prevent these products from overturning and spilling hot water. They believe that this will lead to the manufacture of safer products, and they hope that our work with the relevant parties will help this be adopted as a JIS standard, which will contribute to the overall improvement of safety standards in the industry.
●Running “cross-functional meetings” that transcend department boundaries
Aside from holding meetings for each department, they run “cross-functional meetings” that straddle personnel from various departments, including design, quality control, printing, electronics, and more. These work as a measure to prevent changes in the client’s product materials or composition without the approval of the supplier, as well as allowing them to gather and analyze information on product accidents. This is effective in optimizing the necessary measures to be implemented for all departments, in addition to strengthening inter-departmental relationships.
●Devising caution reminders for consumers to prevent accidents due to misuse
For any information that needs special reminders, rather than limiting precautions to text in a manual, they make sure to place a leaflet where the user will see it when they open the packaging, or find a way to smoothly guide users through how-to videos of the products using a QR code in the manuals. They are devising various ways and trying out ideas to prevent accidents due to misuse before they occur.
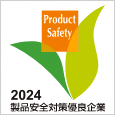
Established | 1964 |
---|---|
Representative | President Hiroaki Kobayashi |
Number of employees | 16,285(consolidated),2,864(non-consolidated)(As of December 2023) |
Location | Nagoya, Aichi |
Business | Development, manufacturing, and sales of water heating equipment, kitchen equipment, and air conditioning equipment. |
URL | https://www.paloma.co.jp/ [external link] |
Reason for Winning
●Designs based on past accidents and thorough safety measures during construction
Once top management realized that “[product misuse] is a dangerous word,” the causes of accidents were thoroughly studied and design measures were improved to prevent accidents due to misuse. In addition, in order to prevent improper installation and repair accidents, they utilize our eight training centers nationwide and conduct safety education regarding repairs and construction for a wide range of customers, as well as provide a thorough safety education for contractors using our very own in-house qualification system.
●Mechanisms to verify product accidents and defects in the event of product recall
Information from every product accident and defect that occurs shall be immediately shared across departments, with a system put in place to understand the details and analyze the root cause, as well as discuss measures to be taken in the event that a product recall might take place. Even in cases where it is decided that there will be no recall, a system shall be put in place to periodically deliberate on the appropriateness of such a decision by a committee made up of outside experts.
●Handing down the lessons learned from past experiences through our “Learning from failures” exhibit
They have an exhibition display in a corner of our headquarters that shows accidents and product recalls that have occurred in the past. They also have a display showing the root cause of the accidents, measures taken, and the lessons they learned. They have made it mandatory for all recently recruited employees or those who are going through a promotion to take a tour of this area to make sure these memories will not fade away with time. In addition, this is also for everyone to relearn the importance of product safety and to continue developing this initiative.
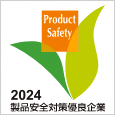
Established | 1948 |
---|---|
Representative | President, Sho Matsumoto |
Number of employees | 236 (As of April,2024) |
Location | Osaka, Osaka |
Business | Development and sales of housing-related materials, Development and sales of materials for senior citizen remodeling |
URL | https://www.mazroc.co.jp/ [external link] |
Reason for Winning
●Realizing both product safety and a circular economy through the MOTOE project
They actively promote the “MOTOE project,” a project that recovers old products for reuse. They replace components and repaint old products, then after inspecting and confirming their safety, they reintroduce them as reusable products. During the repair process, they analyze the deterioration patterns in older products and utilize the information to make improvements and changes to the design in newer models. Through these activities they are able to realize both product safety and a circular economy.
●Continued promotion of a centralized hub for managing product safety information
By collecting all information relating to a product’s design, production, packaging, customer inquiries and complaints, and making it all accessible through a centralized database, they promote a system that makes it possible to prevent reoccurring defects in newly developed items, as well as providing the opportunity to assess similar case studies should accidents ever occur.
●Building a culture of product safety by collaborating with various stakeholders
They are actively building a culture of product safety by collaborating with various stakeholders that are within the circle of their company. This includes holding regular seminars for long-term care businesses that use their products and workshops for their contractors to prevent faulty construction, and a joint study between industry‐academia‐government bodies to investigate real-world product accidents. They will also participate in events to prevent product misuse in local governments with a high elderly population, in addition to using social media to maintain a communication pipeline.
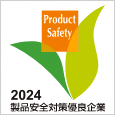
Industrial and Product Safety’s Award OGK KABUTO Co., Ltd.
Established | 1982 |
---|---|
Representative | President: Hiroki Kimura |
Number of employees | 121 (as of September 2024) |
Location | Osaka, Osaka |
Business | Planning, manufacturing, and sale of motorcycle and bicycle helmets |
URL | https://www.ogkkabuto.co.jp [external link] |
Reason for Winning
●Actively raising safety awareness by encouraging the obligatory use of helmets for cyclists
In light of the use of helmets being made mandatory effort for cyclists nationwide in April 2023, they have taken action towards raising awareness by holding work shop at police stations, local governments, and schools in various regions. This is to ensure that people understand the importance of wearing a helmet, as well as the correct way to choose and wear one, which they enact through co-creating awareness videos with local governments and spreading the videos through industry associations.
●Safety verification that take into account long-term outdoor usage and initiatives towards product refinement
Due to helmets being notable for their long-term outdoor use, this has led to a study on designs and selection of materials that are less likely to degrade. This study includes not only proactive initiatives towards advanced safety through joint research with universities, but also accelerated degradation tests beyond the scope of standard requirements and outdoor exposure checks to confirm the functionality of the products and components both before and after exposure.
●Product safety measures based on customer opinion
They internally share information about defects gathered from their customers. Additionally, they strive to design products that prevent potential accidents from occurring by periodically holding TQM activities with multiple departments, including the QA department. To improve their products, they keep an ear out for consumer opinions from the elderly and those that are unfamiliar with using helmets due to increased demand.
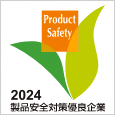
Industrial and Product Safety’s Award TAKAGI CO., LTD
Established | 1940 |
---|---|
Representative | President: Tatsuya Takahashi |
Number of employees | 375(As of April 2024) |
Location | Sanjyo, Niigata |
Business | Planning, manufacturing, and sales of construction tools, power tools, DIY supplies, gardening supplies, etc. |
URL | https://www.takagi-plc.co.jp/ [external link] |
Reason for Winning
●Initiatives to prevent accidents due to misuse using the information gathering system ”CINDY”
All information, such as inquiries from clients about their products, gathered via their website, email, telephone, and other routes shall be managed through the centralized information gathering system “CINDY.” Through this system, and by frequently reviewing the product FAQ on their company website and manuals, they can not only properly organize but also understand the interests, questions and requests of consumers. Additionally, they will work towards preventing accidents due to misuse by informing consumers and helping them understand more about their products.
●Ensuring traceability to prepare for the unlikely event of a product recall and the method of notification
To prepare for the unlikely event of product accidents and defects, they ensure traceability at the component level, such as battery packs, using QR codes, and at the product level using manufacture lot numbers. Additionally, they are building a system to directly and quickly send recall notifications to relevant parties through their official company LINE(mobile messenger application)account.
●Promoting safety measures while continuing to take into consideration top management and our presence in the Tsubame Sanjo region
Under the supervision of our top management, they have begun a project to proactively realize their own measures towards product safety that do not simply meet the industry standards. As they are based in Tsubame Sanjo region, they can utilize the knowledge they gain through our active exchange of ideas with various companies in the area that have also received awards to promote even more progressive safety measures within the industry.
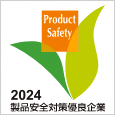
Established | 1988 |
---|---|
Representative | President: Takahiro Narai |
Number of employees | 34(As of November 2024) |
Location | Amagasaki, Hyogo |
Business | Development, manufacturing, and sales of educational toys, as well as the operation of early childhood education classes. |
URL | https://www.ed-inter.co.jp/ [external link] |
Reason for Winning
●Product development that reflects user voices and setting the target age
In order to evaluate and make improvements from a safety perspective using real-life use cases among infants, they have invited a veteran tutor from their nursery into their product planning and design. In addition, they set up a target age range for games and mental training, as well as imposed a strict safety standard in their products to avoid small parts from falling off and causing accidental ingestion.
●Voluntary and continuous improvement of a product based on strong safety awareness
The opinions of their clients are thoroughly collected via emails and phone calls, as well as through their company website. In the event of receiving any information about defects and accidents, the actual product in question is always recovered for root cause analysis. Even in cases where there were no accidents or defects, the results are used in voluntary product improvements from a safety perspective, in addition to being collected in a database for future product development.
●Safety-first craftsmanship in our overseas factory
They are the only Japanese manufacturer of wooden educational toys that has an overseas factory. At this factory they make sure to ensure traceability from material sourcing to the wood processing, coating, inspection, and shipping, as well as dispatch a staff member from headquarters once a month to check the manufacturing process and provide supervision to ensure safe craftsmanship.
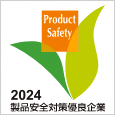
Established | 1943 |
---|---|
Representative | President: Hiromi Seki |
Number of employees | 283(As of October 2024) |
Location | Takayama, Gifu |
Business | Manufacturing and sales of wooden furniture and fittings. |
URL | https://www.kashiwa.gr.jp/ [external link] |
Reason for Winning
●Our own criteria formulation and joint technology based on the features of lumber
Due to the organic nature of lumber, they know that its strength and density can vary. As such, they have formulated their own criteria for size and quantity to find an appropriate range. They are devising methods to prevent accidents due to product fractures by selecting and using materials that meet these criteria. They have developed their very own “S-shaped finger joint” technology, the design of which strengthens the material.
●Supervision by the transport company to prevent accidents due to impact during transit
By analyzing past data related to product accidents, they discovered that the majority were caused by impact during transit. As a result, they distributed handouts requesting that transport, installation, and packing companies exercise greater caution.
Additionally, they visited distribution and delivery sites to observe the actual processes, such as loading and unloading, from assembly to final delivery. Based on these observations, they proposed improvements wherever necessary, which led to accident prevention.
●Initiatives to build a product safety culture that is ahead of industry organizations
As a member company of the Hida Woodworking Federation, they have actively hosted local elementary school students for factory tours for over 30 years to share the proper way to use their products. In addition, they also oversee the development of authentication criteria for the Federation, which includes lumber, coatings, and adhesives.
They have consistently contributed over the years to building a product safety culture that is ahead of industry organizations.
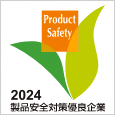
Established | 1919 |
---|---|
Representative | President: Takaaki Izumi |
Number of employees | 297(As of October 2024) |
Location | Tatsuno, Hyogo |
Business | Planning, manufacturing, and sales of school backpacks (randoseru) and related goods, as well as planning and sales of other bags. |
URL | https://www.seiban.com/ [external link] |
Reason for Winning
●Safety measures in designs based on accident trends among elementary students
In order to ensure the safety of elementary students, they gathered information on accidents that occurred while students were using backpacks. Based on accidents that involved students being caught between bus doors, they have taken measures to develop metal fittings that automatically fall off when pulled with a certain amount of force. They also adopted the use of reflector materials to prevent traffic accidents from happening due to low visibility during the evening and at night.
●Operating as an industry leader according to our very own standards of up to 10 years of use
Based on the features of backpacks that are used long-term in various environments, they have formulated our very own 10-year-use standards that extends past the industry standard of 6 years. They only adopt materials (in all color variations) whose durability has been confirmed through their in-house facility that tests for rapid deterioration.
●Monitoring support status using the voices of customers (VOC) and sharing this information with the entire company
They gather complaints and requests from the voices of customers (VOC) that come through our inquiries and allocate the appropriate department to handle any issues. They have setup a system so that the information is shared with the entire company to prevent voices from being ignored or insufficiently handled.
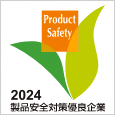
Established | 1964 |
---|---|
Representative | President: Matsunaga |
Number of employees | 109 (As of July 2024) |
Location | Kitanagoya, Aichi |
Business | Manufacturing and sales of nursing and welfare products such as wheelchairs, walkers, stretchers, and canes. |
URL | https://www.wheelchair.co.jp/ [external link] |
Reason for Winning
●Product development on the user perspective
During the development stages of a new product, their main aim is to create a safer product while ensuring basic safety through their own tests and commercial standards. Through the inspection of a prototype by a wheelchair user in our company, they can find issues on a user perspective and feed them back to the R&D department.
●Accumulation of knowledge in our own checklist
Regarding made-to-order products, they summarize any issues that occur during the development process and utilize them for future product developments.
●Company-wide sharing of product accidents and defect information
Any information on product accidents and defects are gathered by the sales personnel through retailers/wholesalers and are registered in our in-house core system so that it is shared by all the relevant parties within our company and utilized to produce safer products.
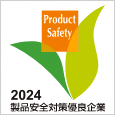
Established | 1992 |
---|---|
Representative | President: Tadahiro Kawatiya |
Number of employees | 140(consolidated), 101(non-consolidated)(As of July 2024) |
Location | Onogi, Fukuoka |
Business | Manufacturing and sales of medical and nursing care beds, mattresses, and related bed accessories. |
URL | https://www.platz-ltd.co.jp/ [external link] |
Reason for Winning
●Ensuring traceability in the production process by utilizing video records
In addition to attaching serial numbers to each material, by having a video recording of the production process they can build a system to confirm at a later time what material was processed when, how, and by who. In the event of a product defect, this will make it possible to identify the cause and discuss measures in accordance with the actual situation.
●4-panel comics as a reminder of nursing product accidents and near-misses
Case studies of nursing bed and stationary handrail accidents and near-misses are summarized in 4-panel comics. They have prepared a guidebook to raise awareness on the proper usage and selection of products and distributed it among medical and nursing workers, as well as among their company customers and general consumers in order to prevent accidents when using nursing products from occurring.
●Sharing accident information at an industry organization level and re-examining our products
As a member of the Safety Promotion Council for Medical and Home Care Bed, they join the activities and share information on why and how significant product accidents occur. Utilizing what they can learn about accident information on another company’s product, they can risk assess whether or not their own product may suffer a similar fate, and as such they can work towards redesigning it if they deem it necessary.
Retailer Category
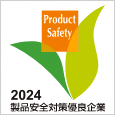
Industrial and Product Safety’s Award Daiichidenkasha.Co
Established | 1967 |
---|---|
Representative | President: Takashi Ueda |
Number of employees | 36(AS of October,2024) |
Location | Tenri, Nara |
Business | Import and sales of espresso machines, and coffee bean roasting. |
URL | https://daiichi-mottainai.com/ [external link] |
Reason for Winning
●Measures against changes in component materials or specifications without notification based on past experience.
They have learnt a lesson from experience that suppliers occasionally change component resin materials without prior notice and have decided to take measures against such changes.
They identify components that are especially significant from a safety perspective and create an inspection checklist to see any unwarranted deviations from the specifications.
With the checklist, they implemented a two-tiered approach: one for sampling inspection on receipt of goods and the other for total inspection before shipment, and they make sure to keep a record of the entire process.
●Sharing product safety information via expository videos covering a wide range of themes
They create videos that give crucial information sorted by themes, such as proper maintenance and trouble-shootings, as well as a basic understanding of voltage and electrical power supply. These informative videos are easily accessible to their customers both on our company website and with a QR code on leaflets included in a product box.
●Their continuing activity to enhance their company value, originating in product safety
They consider product safety measures as operations to improve the value of their company not as cost, thus they proactively devise countermeasures, disseminate their efforts widely, which would reinforce the credibility of their brand and extension of their market, and which eventually generate a synergistic effect such as the revitalization of their company with new talent.
Sharing their success stories with outside parties, they are hoping to create a socially virtuous cycle.
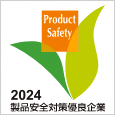
Established | 1991 |
---|---|
Representative | President: Kazuyuki Ido |
Number of employees | 50 (As of October 2024) |
Location | Yamatokoriyama,Nara |
Business | Sales, inspection, and repair of residential equipment. |
URL | http://www.nara-nikka.com/ [external link] |
Reason for Winning
●Quick and proper aftercare via a customer management system
Traditionally, customer information was managed by each sales branch. By centralizing the management of customer information within a system shared by the entire company, any time an inquiry is made by a customer they can look back through the purchasing and repair history of the product to quickly and accurately provide repair support. In addition, they can even propose that a product be replaced due to it being past its life cycle, thereby allowing them to prevent product accidents from happening beforehand.
●Publicizing recall information to regional customers through our own intermediaries
The “Nikka Tuushin” newsletter is distributed once every 2 months to all our customers, regardless of the product sold by our company, and includes a wide array of recall information that is to be publicized by the manufacturer in order to prevent an increase in product accidents.
●Continuing product safety activities through the community-based “Anshin-club”
Since 2000, they have been carrying out the “Anshin-club,” a membership-based safety support system for local residents. This provides a maximum of up to 6 visitations for approximately 500 households to make sure that products are being used safely. In addition, they offer consultations for maintenance such as cleaning, as well as replacements when products have been used for a long time.
Retailer Category
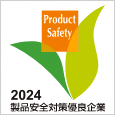
Established | 1971 |
---|---|
Representative | President: Kenji Endo |
Number of employees | 488(As of March 2024) |
Location | Kanazawa,Ishikawa |
Business | Development, design, and manufacturing of electronic control units and remote controls (for gas, oil, and electric appliances), high-voltage units, and LED lighting. |
URL | https://www.rbcontrols.co.jp/ [external link] |
Reason for Winning
●Implementation of multiple measures for product safety considering the characteristics of components
They take various measures to achieve the advanced quality and safety required for electronic control units of gas appliances.These include evaluating the safety of electronic components during failure using FMEA and stipulating in the standard design documents a system for ensuring safety through software, assuming a malfunction of the microcontroller.
●Aggregation of past troubles relating to Lessons Learned for the prevention of recurrence
The details, causes, and measures of past troubles are summarized in the Technical Issue Reflection Checklist (Lessons Learned).During the product development and design stages, they refer to this checklist to ensure that there are no repeated mistakes or oversights.This enables them to implement exhaustive measures to prevent recurrence.
●Educational programs aimed at promoting knowledge on product safety and its dissemination.
They have established a hierarchical education program for engineers to learn about the importance of product safety and related laws, as well as an education program aimed at standardizing the knowledge and skills necessary for product design.These are programs to take within two years after their assignment.
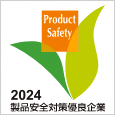
Established | 1973 |
---|---|
Representative | President: Hideki Masaki |
Number of employees | 4(As of October 2024) |
Location | Osaka,Osaka |
Business | Businesses utilizing AI for risk assessment, product safety design, standardization of instruction manuals, and safety digital transformation (DX). |
URL | https://www.koshida-art.co.jp/ [external link] |
Reason for Winning
●Developing risk assessment methods that utilize AI
By using AI to implement correlation analysis of the text information in the accident information database, they can develop a platform that extracts hazards related to a special product. Since this will make risk assessment possible within the short time allotted rather than doing it manually, this will contribute towards a safer form of craftsmanship.
●The contribution to the formulating a standard regarding manuals and publicizing the content
When formulating a draft of a industrial standard (JIS B 9719:2022) for the creation of a manual, they contribute to this as a committee and WG member, as well as individually holding workshops to explain these standards to Japanese manufacturers and publicizing the content.
●Continued initiative support towards PS Awards' community companies
They continue to provide and increase our support for initiatives taken by Japanese companies regarding PS Awards. This includes design reviews and risk assessments of products developed by companies within or out of the PS Awards' community who were awarded a PS award, evaluations and inspections of manuals, branding that takes measures towards product safety, and more.
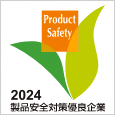
Established | 2016 |
---|---|
Representative | President: Michiko Nakahara |
Number of employees | 1(As of November 2024) |
Location | Amagasaki, Hyogo |
Business | Providing tools and services for those who face challenges when going out with children (assessment-based sales of the product named "Futago Jitensha"). |
URL | https://futago-jitensya.jp/ [external link] |
Reason for Winning
●Initiatives to prevent product accidents by “assessment-based selling”
Using their own system of “assessment-based selling,” they can prevent accidents from happening beforehand. For example, for an individual wanting to purchase a three-wheeled bicycle for two infants to ride, they can show the merits and demerits of such a product in order to ensure that the user and the product are a good match, or provide an opportunity to show the safety risks involved regarding the possible environments where the product will be used, such as near their home or roads.
●Preventing accidents beforehand or from reoccurring by utilizing user interaction and contributing to product enhancement
When providing an assessment, they analyze and organize the information on overturning accidents that were gathered when interacting with the user. By publicizing the incident on their company website they can not only prevent accidents from happening beforehand or from reoccurring, but also provide feedback to bicycle manufacturers pertaining to the usability of their products and defects that relate to safety, which will enhance and contribute to further product development.
●Raising safety awareness through seminars at company events and for local governments
At the lectures they hold on choosing bicycles, they offer words of caution when choosing and using bicycles that children ride, regardless of whether they are two-wheeled or three-wheeled. Additionally, in seminars requested by local governments, they are raising safety awareness amongst a wide range of consumers by openly talking about topics such as proper helmet usage and maintenance, or how to prevent overturning.
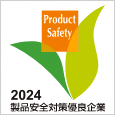
Established | 2000 |
---|---|
Representative | President: Jasper Cheung |
Number of employees | 14,000(As of October 2024) |
Location | Meguro, Tokyo |
Business | Electronic commerce business utilizing the internet and other platforms, services for listing on e-commerce sites, and logistics operations. |
URL | https://www.amazon.co.jp/ [external link] |
Reason for Winning
●Upgrading an initiative that is based on the foundation of a product safety management system
When adopting a new product safety management system, they offer initiatives such as monthly risk reviews that study product safety issues from multiple angles, such as opinions of consumers and sales agents, in addition to in-house standardization of knowledge regarding product safety.
●Improving recall notifications for consumers
They have established a new team to investigate risk awareness, consumer behavior, and potential risks through questionnaires. By analyzing all this information, they make an easy to view recall notifications system on our website or an app.
●Continuing to offer and further expand the “Anshin Mail” service that offers product safety information to customers
They are collaborating with various organizations such as the National Institute of Technology and Evaluation (NITE) to continue and expand the “Amazon Anshin Mail” service that provides customers that have purchased products from a certain category with safe usage notifications. In addition, they are expanding this service to stores in the USA, Canada, Europe, and more.
Although the company is a leading online mall company and has been implementing new initiatives and improvements since their latest award in 2021, due to their large platform which quickly provides an enormous volume of trade, we hope that they will take a proactive approach towards preventing illegal goods, including those that are at risk of being illegal, from showing up on the platform.