-
- 政策について
- 白書・報告書
- 製造基盤白書(ものづくり白書)
- 2020年版
- HTML版
- 第1部第1章第3節 製造業の企業変革力を強化するデジタルトランスフォーメーション(DX)の推進
2.設計力強化戦略
第1部 ものづくり基盤技術の現状と課題
第1章 我が国ものづくり産業が直面する課題と展望第3節 製造業の企業変革力を強化するデジタルトランスフォーメーション(DX)の推進
2.設計力強化戦略
(1)品質・コストの8割は設計で決まる
次に、デジタル技術によるエンジニアリングチェーンとサプライチェーンの連携の意義について議論するが、その前提として、エンジニアリングチェーンの重要性について、改めて確認する必要がある。
製造業では、製品の品質とコストの8割は、設計段階で決まると言われてきた。
図132-1は、仕様変更の自由度と品質・コストの確定度を示したものである。開発が進むに従って製造設備などが確定していくため、仕様変更の自由度は低下し、設計が完了した後の仕様変更の余地は極めて限定的なものとなる。その結果、仕様変更の自由度が高い設計段階で、製品の品質とコストの8割程度が決まることになるのである注4。
注4 日野三十四『実践 エンジニアリング・チェーン・マネジメント:IoTで設計開発革新』(2017年、日刊工業新聞社)
このため、できるだけ開発の初期段階であるエンジニアリングチェーンに資源を集中的に投入すること(「フロントローディング」注5)により、問題点の早期発見、品質向上、後工程での手戻りによるムダを少なくすることが決定的に重要になる(図132-2)。
注5 設計初期の段階に負荷を掛け、作業を前倒しで進めること。
その上、近年、グローバル化、顧客の製品機能要求の高度化・多様化、環境制約・資源制約の先鋭化といった傾向が高まっている。特に、2015年9月の国連サミットにおいて「持続可能な開発目標(SDGs)」が採択されたことで、企業が果たすべき社会的役割に注目が集まり、我が国製造業企業にも対応が求められている。製品に対する機能要求が高まる一方で、制約条件が厳しくなるのであれば、製品は一層複雑化することにならざるを得ない。
また、製品に占める制御ソフトウェアの比率が高まっていることも、製品の複雑化を招いている。この傾向は自動車において特に顕著である。自動車ソフトウェアのコード数は、2000年時点では100万行程度であったが、現在では1億行を超えている。F-35戦闘機が2000万行、Microsoft Office 2013が4,400万行と言われているので、自動車ソフトウェアの複雑さは突出している注6。
このように製品が複雑化していけばいくほど、エンジニアリングチェーンに掛かる負荷はより大きなものとなる。すなわち、製品の複雑化が進めば進むほどに、それに対応できるエンジニアリング能力の高さこそが、製造業の競争力を左右するといえる注7。
注6 経済産業省「自動車新時代戦略会議(第1回)資料」内参考資料P11(平成30年4月18日)
注7 藤本隆宏編『「人工物」複雑化の時代:設計立国日本の産業競争力』(2013年、有斐閣)
さらに、第2節で論じたように、近年、世界的に不確実性が高まっており、我が国の製造業は、この不確実性にも対応しなければならなくなっている。より具体的にいえば、想定外の突発的な環境や状況の変化が発生した場合、製品の仕様を早急に変更しなければならないというリスクにさらされているのである。例えば、このような事態に対しては、仕様変更の自由度が高い設計段階において対応せざるを得ず、しかも可能な限り迅速に対応することが重要である。さらに仕様変更に対応する「製品設計」のみならず、仕様を変更した製品を効率的に製造できるよう、製造工程を迅速かつ自在に変更するための「工程設計」の能力も必要となる。
このように、不確実性に対応するには、製品設計と工程設計の双方を含むエンジニアリングに高い能力があることが求められる。エンジニアリングの能力は、製造業が不確実性に対応するダイナミック・ケイパビリティの中核を占めるものといえる。
(2)我が国の製造業のエンジニアリングチェーンの現状と課題
それでは、我が国製造業のエンジニアリングチェーンは現在どのような状態にあるのだろうか。
2019年12月に国内製造業に対して実施されたアンケートによれば、エンジニアリングチェーンの上流に当たる製品設計力のここ5年間での変化の状況について、約4割が向上していると答えたものの、半数以上が「あまり変化は無い」と回答している(図132-3)。製品設計のリードタイムに関しても同様で、約4割が短くなっていると回答した一方で、半数以上が「あまり変わらない」としている(図132-4)。製品設計のリードタイム短縮を図るための取組として重視しているものを確認すると、半数以上が「生産技術、製造、調達といった他部門との連携促進」と回答しており、設計力の強化に向けては他部門との連携が重視されている(図132-5)。
図132-5 製品設計のリードタイム短縮を図るための取組として重視しているもの
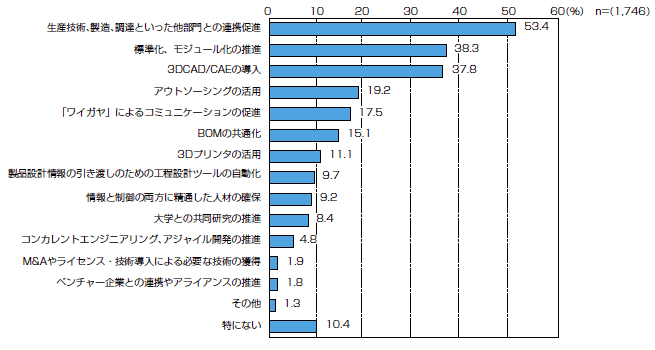
資料:三菱UFJリサーチ&コンサルティング(株)「我が国ものづくり産業の課題と対応の方向性に関する調査」(2019年12月)
また、国内製造業に対して工程設計(生産技術)力のここ5年間での変化について尋ねたところ、36.9%が「向上している」、58.8%が「あまり変化はない」、4.3%が「低下している」と回答した(図132-6)。
図132-6 工程設計力の5年前に比べての変化
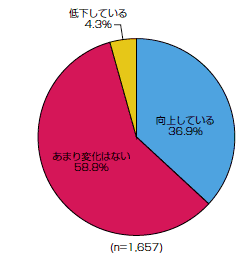
資料:三菱UFJリサーチ&コンサルティング(株)「我が国ものづくり産業の課題と対応の方向性に関する調査」(2019年12月)
工程設計力が「向上している」と回答した企業に対してその要因を確認したところ、「生産技術、製造、調達といった他部門との連携強化」と回答した企業が最も多く79.2%を占め、「営業、アフターサービスなどから顧客ニーズのフィードバックを強化(26.5%)」「デジタル人材の育成、確保(22.5%)」が続いている(図132-7)。
図132-7 工程設計力が向上した理由
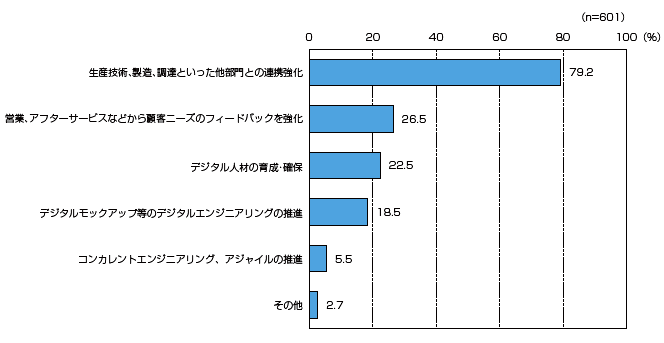
資料:三菱UFJリサーチ&コンサルティング(株)「我が国ものづくり産業の課題と対応の方向性に関する調査」(2019年12月)
一方、工程設計力が「低下している」と回答した企業についても同様にその要因を確認すると、「ベテラン技術者の減少(79.4%)」、「製造現場との連携不足(30.9%)」、「属人的な設計プロセス(25.0%)」、「間接部門の人員削減(19.1%)」が上位に挙がっている(図132-8)。この結果から、工程設計力の維持が熟練者の技に頼りがちで、その技術を後継に引き継ぐことが課題となっている様子がうかがえる。また、他部門との連携は、向上・低下双方の要因として上位に挙げられており、他部門との協調が工程設計力強化の鍵であることが分かる。
図132-8 工程設計力が低下した理由
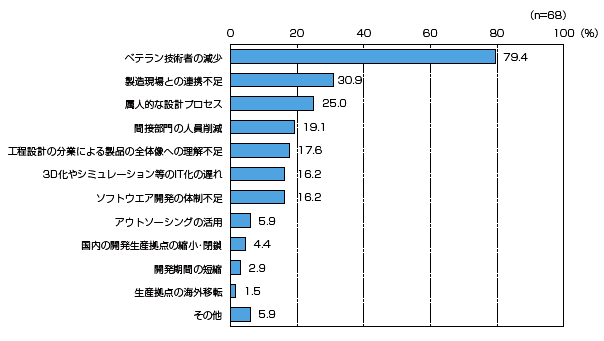
資料:三菱UFJリサーチ&コンサルティング(株)「我が国ものづくり産業の課題と対応の方向性に関する調査」(2019年12月)
そこで、国内製造業における製品設計、工程設計、製造等の部門間の連携状況を見ると、「ある程度連携がとれている」と回答した者が72.1%を占め、自社の部門間連携に対して課題と感じていない者が多数を占めている(図132-9)。
図132-9 製品設計、工程設計、製造等の部門間の連携状況
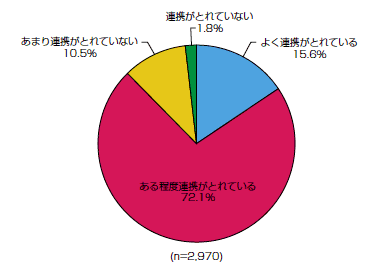
資料:三菱UFJリサーチ&コンサルティング(株)「我が国ものづくり産業の課題と対応の方向性に関する調査」(2019年12月)
一方で、「あまり連携がとれていない」もしくは「連携がとれていない」と回答し、部門間連携に課題を感じている企業に対して、それにより生じる課題や問題を聞くと、「品質不良が発生する(55.5%)」「設計変更が製造に伝わらないことがある(42.8%)」「正確なコスト予測ができない(39.4%)」といった回答が上位に挙がった(図132-10)。
図132-10 連携不足による課題や問題
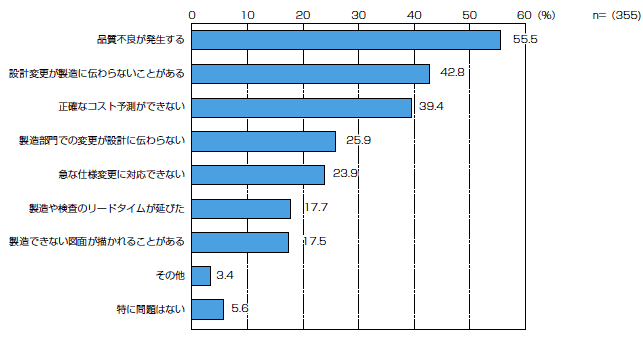
資料:三菱UFJリサーチ&コンサルティング(株)「我が国ものづくり産業の課題と対応の方向性に関する調査」(2019年12月)
我が国製造業における品質不正の問題については、2017年10月以降、製品検査データの書き換えなどの不正事案が複数発覚した。品質保証体制の在り方は企業の競争力に直結する経営問題であり、また、サプライチェーン等を考慮すれば、我が国製造業全体の競争力にも影響を及ぼしかねない。部門間における連携が不足していることが品質不良につながっており、早急な解決が必要である。
また、製品設計力や工程設計力の伸びと部門間の連携状況との関係を見ても、部門間の連携がとれている企業ほど、製品設計力、工程設計力が向上する傾向にある(図132-11・12)。
(3)部門間・企業間のデータ連携
すでに述べたとおり、エンジニアリングチェーンを強化する上では、設計、製造、調達といった各部門との連携を強化することが有効である。しかし、実際には、企業内部において、設計部門と製造部門の間のコミュニケーションが十分に行われていない場合がある。また、設計部門と製造部門が、それぞれ異なるITベンダーから異なるITシステムを導入しているため、両部門のシステムの連携が必ずしもうまくいっていないという場合もある。
設計部門と製造部門の連携が不十分な場合には、先ほどのアンケート結果からも推察されるとおり、
- 設計部門のデータと製造部門のデータの変換処理に膨大な工数や処理時間が掛かる
- 作業工程・設備・治工具などの製造現場の情報が設計仕様に反映できないために製造現場に過度な負担が掛かる
- 当初見込まれなかった製造や調達のコストや作業などの情報が設計側に反映されない
- 設計部門と製造部門の伝達のミスが発生しやすく、両部門間の打ち合わせを頻繁に行わなければならない
などの問題が生じる。これらの問題は、製品の複雑化や不確実性の高まりによっていっそう深刻化し、製造業の競争力にとって致命的なものとなりかねない。
エンジニアリングチェーンとサプライチェーンを連携させるために必要な第一歩は、設計部門が設計を行う上で使用する設計部品表(E-BOM注8)、製造部門が製造を行う上で使用する製造部品表(M-BOM注9)、そして工程設計情報をまとめたものである工程表(BOP注10)を結びつけて、各部門がこれらを共有することである。
これにより、設計部門から製造部門、あるいは製造部門から設計部門への双方向の円滑なデータ連携が可能となる。例えば、設計変更による製造現場への影響範囲を確認しながら設計を行ったり、あるいは生産管理を変更したりすることが容易になる。さらに、製造部門から、原価実績情報も含めた製造情報を設計部門にフィードバックすることで、設計段階で精度の高い原価企画やシミュレーションを行うことも可能になる注11。加えて、部門を超えたデータ連携により部門間の連携が強化されることで、品質不良の削減につながり、ひいては我が国製造業における品質保証体制強化と生産性向上の両立を実現することが期待される。
注8 Engineering Bill of Materials
注9 Manufacturing Bill of Materials
注10 Bill of Process
注11 羽田雄一『IT活用で製造業に革命を起こすものづくりデジタライゼーション』(2018年、幻冬舎メディアコンサルティング)
なお、第2節2.(4)で論じた「柔軟な組織」は、権限や部門を横断した連携やコミュニケーションをより円滑に行うことができ、高いダイナミック・ケイパビリティを発揮できる組織である。部品表や工程表の整備は、そうした部門を超えたデータ連携を容易にすることで、組織を柔軟にし、ダイナミック・ケイパビリティを高めるものである。
さらに、このようなデータの連携と双方向のコミュニケーションは、設計部門と製造部門のみならず、企業全体、さらには企業組織の枠をも超えてサプライヤーや顧客などの間でも実現することで、いっそう大きな威力を発揮するであろう。
このことは、第2節2.(5)で論じたサプライチェーンの柔軟性等を高める上でも、極めて重要である。というのも、仮に不測の事態が勃発して、ある国の生産拠点が停止せざるを得なくなった場合、生産を別の工場において迅速に代替できれば、供給途絶は回避できる。しかし、設計部品表、製造部品表、工程表が統一的に整備され、共有されていない場合は、代替生産を開始する際に部品表から調整しなければならないため、膨大な人員と作業を要することになる。これでは、柔軟かつ迅速な代替生産を行うことは不可能である。このように、サプライチェーンの柔軟性等を高め、ダイナミック・ケイパビリティを強化するためには、実は、部品表や工程表を整備し、エンジニアリングチェーンとサプライチェーンを連携させておかなければならないのである。
新型コロナウイルス感染症の感染拡大を契機に、グローバル・サプライチェーンの強化の必要性が改めて認識されているが、強靭なサプライチェーンを構築するためにも、部品表や工程表を整備し、エンジニアリングチェーンを強化することが不可欠なのである。
(4)バーチャル・エンジニアリング
1990年代半ば以降、製造業の設計現場に3DCAD(Computer Aided Design)の導入が始まった。2000年以降になると、CAM(Computer Aided Manufacturing)にCAE(Computer Aided Engineering)が加わるようになり、さらにPDM(Product Data Management)によって、設計・製造・解析の各データを同期させて一体に検討する「バーチャル・エンジニアリング」の環境が整備されていった。最近では、これにIoTやAIが加わり、バーチャル・エンジニアリングは更なる進化を遂げつつある。
このバーチャル・エンジニアリングにより、企画、設計、製造、営業、品質、認証等の各分野の専門家、さらにはサプライヤーや一部顧客までも含めて、3D図面を用いて同期的・一体的に製品開発に参加することができる協業の場が実現する。また、バーチャル・エンジニアリングを用いることで、構想設計の段階で、検証も含めた詳細設計までが可能になり、リアルな試作の前に全ての仕様を決めることができるので、製品開発のリードタイムは、大幅に短縮することとなる。このようなエンジニアリングの手法は、「コンカレント・エンジニアリング」「サイマルテニアス・エンジニアリング」とも呼ばれる。
ダイナミック・ケイパビリティ論に即していえば、バーチャル・エンジニアリングは、機会を捉え、既存の組織内外の資産・知識・技術を再構成して競争力を獲得する「捕捉」の能力を著しく高め、開発リードタイムを極限まで短縮化する。こうして、バーチャル・エンジニアリングは、不測の事態に迅速に対応する能力であるダイナミック・ケイパビリティを著しく高めるのである。
従来、日本の製造業は、製造現場の技術力(いわゆる「匠の技」)が非常に高く、それが競争力の源泉となっていた。このため、設計部門から送られてきた設計図面が多少不備であっても、製造部門の技術者が、設計図面を細かく修正したり、詳細部分を設計したりすることができた。日本の製造業では、生産設備を考慮に入れた量産品質の高い最適仕様の設定は、設計部門ではなく、製造部門において行われる傾向にあったのである注17。
注17 内田孝尚『バーチャル・エンジニアリング-周回遅れする日本のものづくり』(2017年、日刊工業新聞社)
しかし、近年、製品の複雑化が進み、さらには不確実性が高まる中で不測の事態への俊敏な対応も必要になる中では、これまでのように、詳細設計まで製造現場の技術力に過度に依存することは、極めて難しくなっている。加えて、近年、生産年齢人口の減少等により、熟練技術者が減り、生産現場の技術力の維持・向上にも支障を来しつつある。このようなことから、製造業が競争力を維持し強化する上では、バーチャル・エンジニアリングは大きな役割を果たすものと考えられる。ところが、我が国の製造業では、バーチャル・エンジニアリングが進んでいないことが、今回の調査で浮き彫りとなった。
バーチャル・エンジニアリングでは、3DCADを用いて設計図面を描くだけにとどまるものではなく、設計情報の受け渡しも3Dデータで行うことが基本となる。ところが、3Dデータのみで設計を行っているのはわずか17.0%にとどまっている(図132-13)ことに加え、協力企業への設計指示の半数以上が未だに図面で行われ、3Dデータによる指示は15.7%に過ぎない(図132-14)。また、3Dデータによる指示を行わない理由の約半数が、「主な設計手法が3Dではないため」と答えている(図132-15)。
図132-15 2Dデータや図面で設計指示している理由
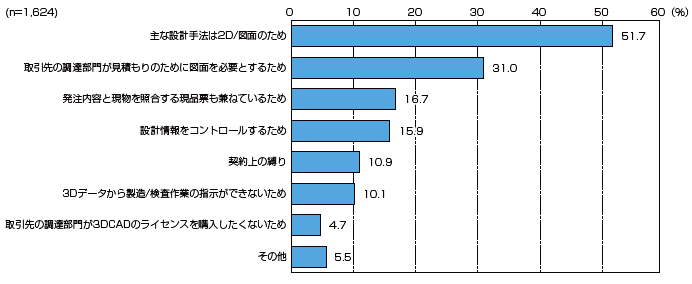
資料:三菱UFJリサーチ&コンサルティング(株)「我が国ものづくり産業の課題と対応の方向性に関する調査」(2019年12月)
関連して、一般社団法人日本自動車工業会が同工業会に加盟する自動車会社に対して行った調査(図132-16)によれば、全体的に、2D図主体から3D図主体への移行は停滞しており、直近では、3D図から2D図への回帰の傾向すら現れている。また、3D図面化を進めようとしている企業と、2D図主体を維持しようとする企業との二極化が拡大している。
図132-16 2018年度3D図面普及調査レポート(JAMA各社の状況)
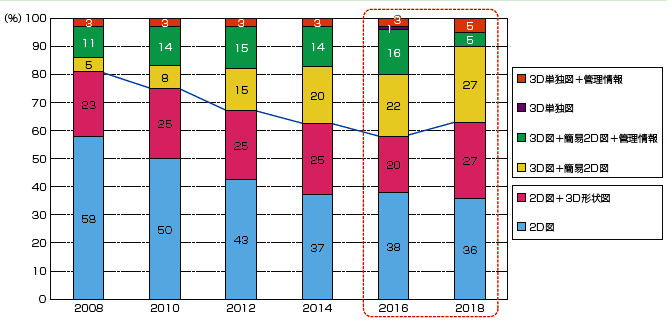
資料:三菱UFJリサーチ&コンサルティング(株)「我が国ものづくり産業の課題と対応の方向性に関する調査」(2019年12月)
しかし、3DCADを利用しバーチャル・エンジニアリングを進めることはエンジニアリングチェーンの強化に不可欠である。アンケートを見ても、3DCADを利用した設計が進んでいる企業ほど、製品設計力が向上し、製品設計のリードタイムが短縮している(図132-17・18)。さらに、工程設計力も向上している(図132-19)。アンケートの結果からも、3DCADの利用がエンジニアリングチェーンの強化に大きく貢献することが分かる。
図132-19 工程設計力の5年前に比べての変化と設計方法の関係
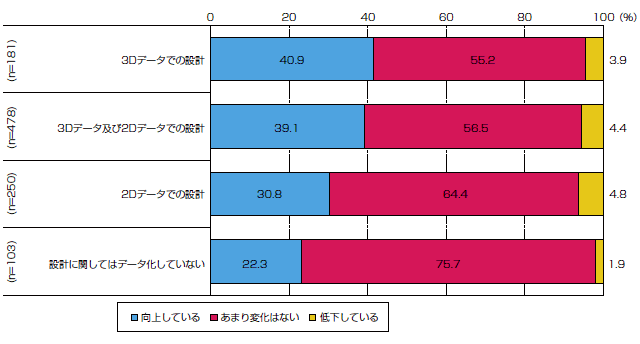
資料:三菱UFJリサーチ&コンサルティング(株)「我が国ものづくり産業の課題と対応の方向性に関する調査」(2019年12月)
以上で見てきたように、我が国の製造業では3Dによる設計が未だに普及しておらず、バーチャル・エンジニアリングの体制が整っていない。不確実性が高まり、製造業のダイナミック・ケイパビリティの重要性が増している中で、このバーチャル・エンジニアリング環境の遅れは、我が国製造業のアキレス腱となりかねないと言っても過言ではない。
(5)マテリアルズ・インフォマティクスの波
2.(4)のバーチャル・エンジニアリングは、主として、自動車産業や電機産業などのディスクリート系(加工組立系)の製造業における製品設計を念頭に置いた議論である。しかし、デジタル技術の威力は、化学産業などのプロセス系の製造業における製品設計にも及んでいる。
特に注目すべきは、情報科学を活用した研究開発である。このような手法は創薬研究の効率化が求められる製薬業界における「バイオインフォマティクス」に見られるように、研究開発を大きく前に進める可能性がある。例えば、創薬研究の臨床開発フェーズでは、ビッグデータ解析を通じて病気の発症や進行に密接に関係する遺伝子変異や生体分子「バイオマーカー」によるターゲットの絞り込みを行うことが有効になる。そして、近年、同様の研究開発手法を素材分野へ適用する動きが活発化してきており、AIやビッグデータを素材分野に適用する、いわゆる「マテリアルズ・インフォマティクス」が注目を集めてきている。マテリアルズ・インフォマティクスは、もともとアメリカで始まり、2011年のオバマ政権下で始まったマテリアルズ・ゲノム・イニシアチブ(MGI)が端緒と言われている。2012年には、MGIに取り組む研究者らが、日本が発表した電池材料に関する論文情報をもとにインフォマティクス的な手法を活用して電池材料開発を行い、日本企業が実験的に見出した結果と同等の結果を論文発表した。これは、実験をせずにデータ分析のみで材料を導き出した点で非常に注目を集めた。その他、欧州、中国、韓国等においても様々な取組が行われている。
日本においても、2013年に内閣府主導の戦略的イノベーション創造プログラム(SIP)において始まり、産学官連携による分野横断的な基礎研究から実用化・事業化までを見据えて一気通貫で研究開発を行っている。また、2015年には文部科学省の情報統合型物質材料開発イニシアチブ(MI2I)において、各種材料の具体的テーマに取り組むとともに、データ駆動型の研究手法の開発に取り組み、産官学の研究者や技術者が研究開発の現場で活用できる情報統合型物質探索・材料開発システムの構築を行っている。
また、経済産業省においては、2016年からの予算事業において、有機系の機能性材料の実験やシミュレーションによって創出したデータをマテリアルズ・インフォマティクスと融合し、革新的な機能性材料の創成・開発を加速させることを目指しており、2019年4月にはシミュレーターの公開も実施した。
一般に、マテリアルズ・インフォマティクスの活用には、質の良い多くの技術データが必要と言われている。このような技術データとしては、民間企業が日々の研究開発活動の一環として独自に蓄積・保有しているものも多いが、学術論文や特許文献等の公知情報も技術データの宝庫であり、協調領域としてデータを整理することは有効であると考えられる。特に特許情報の整理は民間企業の関心も高く、文献を技術分野ごとに整理することも可能であることから、2019年12月より、民間企業や公的研究機関とともに特許情報を活用するためのデータベースの構築及び持続的な活用のための仕組み作りの検討を開始した。化学系企業など20者近い参画者が集まり、検討を進めている点において、これまでにないマテリアルズ・インフォマティクスに関する取組として高い注目を集めている。
このような施策の連携等を通して、世界において高いシェアを確保してきた機能性材料を始めとする素材分野において、研究開発現場でマテリアルズ・インフォマティクスを活用し、日本がその研究開発力を維持・強化できるように、必要な基盤構築を支援していく。