-
- 政策について
- 白書・報告書
- 製造基盤白書(ものづくり白書)
- 2020年版
- HTML版
- 第1部第2章第1節 デジタル技術の進展とものづくり人材育成の方向性
- 4.デジタル技術の進展に対応するものづくり企業の取組
第1部 ものづくり基盤技術の現状と課題
第2章 ものづくり人材の確保と育成第1節 デジタル技術の進展とものづくり人材育成の方向性
4.デジタル技術の進展に対応するものづくり企業の取組
ここまで、ものづくり産業における、デジタル技術活用の取組状況や課題を確認してきた。
高い技術を誇り、日本経済を支える製造業を、引き続き良質な雇用の場とし、日本の成長力の源泉としていくため、今後も企業の生き残り・発展に重要な役割を果たすものづくり人材の育成を強化していくとともに、デジタル技術活用の取組を進め、労働生産性の向上と、高付加価値のものづくりを実現していくことが重要である。
以下では、実際に現場で行われているデジタル技術の活用、良好な人材育成の推進事例、熟練技能の継承の取組などについて紹介する。
(1)労働生産性の向上と働き方改革が進んだ好事例
株式会社オシタニプレス(大阪府堺市)は、従業員8名で、製造現場のデジタル化に取り組む。同社は1975年に創業し、精密板金・プレス加工業を営んでいる。主に大手空調機器メーカーから、部品などの製造を請け負っており、顧客から周期的に依頼のある多品種少量ロットの金属部品を、短期間で生産できることに強みをおく。
品質・機能・デザインなど、顧客によってニーズが異なる製品を手掛ける上で重要なことは、常に稼働状況を可視化(見える化)し、適切に「進捗管理」を行うことであると押谷代表は語る。適時進捗を把握できることで、顧客に正確な納期、進捗を伝えることができ、顧客満足に繋がる。
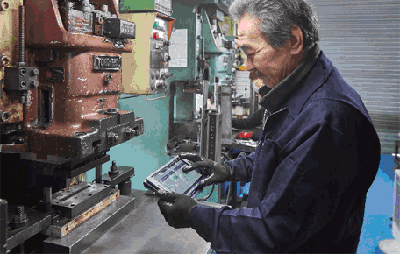
写真:進捗管理システムへの入力の様子
同社では、過去に「進捗管理」に頭を悩ませていた。社屋の1階に工場、2階に事務所があり、事務所からは工場の様子が確認できなかった。そのため、顧客から進捗に関する問い合わせを受けた際には、工場と事務所を何度も往復する必要があった。また納品書や作業指示は、紙面のやりとりで行っていたため、各工程の進捗状況について混乱してしまうことが多かった。そのため、以前は受注の総量が正確に判断できず、業務過多になってしまうことも多く、従業員の残業によってなんとか乗り切っていた状況であった。
そこで、押谷社長はこうした問題を解決しようと、受発注と連携して現場に情報を流す「進捗管理システム」を導入する決意をした。受注データをシステムに取り込み、AIを使って基準在庫や過去の作業実績のデータ解析を行い、生産計画に反映させる。製造機に取り付けたタブレット端末から進捗を入力できるようにし、正確に進捗状況を確認できるようになった。この結果、顧客から引き合いがあった時点で、抱えている生産計画と負荷状況を確認できるようになったため、納期の交渉も可能となり、現場に過度な負担をかけることが少なくなった。また、現場の稼働状況に応じた生産計画を立てることが可能となったことで、生産効率が向上し、システム導入前後で同じ部品を製造した従業員の作業時間が2時間ずつ削減でき、労働環境の改善がみられたという。
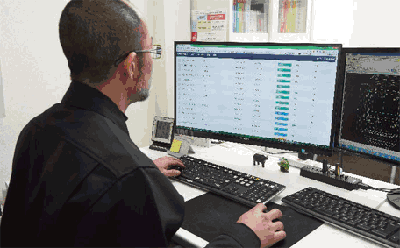
写真:現場で入力されたデータは事務所ですぐに確認し、作業指示などを行う
システムの導入当初は戸惑う声もあったというが、ベテラン社員の積極的な協力もあり、次第に社内へ浸透していった。ベテラン職人の「カン」や「コツ」に依存していた作業もデータとして残せるようになったため、同じ製品の受注が再度あった際には、過去の作業履歴を活用し、効率的に生産が可能となった。押谷社長は「生産性が上がって残業が減ったことで、社員の満足度も上がった。定時の終業時間までにどこまで業務を進められるか考えている。」と語る。
同社は、今後も会社の成長に合わせて製造現場のデジタル化を進め、付加価値の高い製品をつくることを主眼におき、少数精鋭で生産性の高いものづくりを目指していく。(取材日:2019年10月29日)
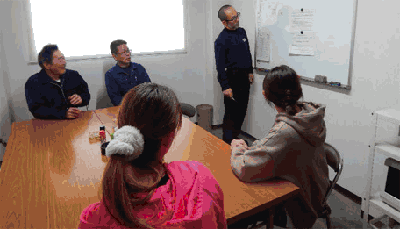
写真:社内勉強会の様子
ダイニチ工業株式会社(新潟市南区)は1964年に石油バーナーや石油ふろ釜のメーカーとして創立され、業界初となる全自動の業務用石油ストーブの製品開発をはじめ、安全で高性能な家庭用石油ファンヒーターや加湿器などを開発し、現在では石油暖房機器については約140種類を製造販売している。
一般的に、暖房機器や加湿器は、季節商品であるため冬季に需要が高くなり、天候によっても受発注が大きく変動することから、同社は、つくり過ぎず、品切れさせないよう年間を通じた平準化生産と受注した当日でも生産計画を変更して製造できる体制を構築している。売れ筋商品は計画的な生産ができるが、天候や市場の動向によって受注量が変動するような商品は、受注後、いかに早く店頭に商品を提供できるかがカギであり、この受注ラインの自動化と作業工程のスピードアップが課題であった。このため、IoT技術を活用した自動化、ロボットの導入や生産ラインの業務効率化を図ることで、受注から4時間で製品の工場出荷を可能にする「ハイドーゾ生産方式」を確立した。
自社が開発した生産管理システムは、工程ごとにクローズした情報のやり取りを越えて、社内の生産管理部門や製造ラインと生産計画情報や稼働状況データのほか、製品ごとの在庫状況や市場での販売状況のデータを横断的に共有して見える化を行うとともに、同システムを協力工場にも展開して一体的に導入することで、受注後から資材の供給調達、プレス加工、塗装、組立、出荷情報まで、すべての工程の稼働状況が画面上でリアルタイムに把握できるようになった。また、同社工場内の重量のある部品の移動は自動搬送機を導入して運搬作業を無人化したほか、組立ラインのネジ止め作業のロボット化や、AI技術による画像検査システムを導入して、部品に装着するリード配線の固定状況を検査する工程を自動化し、省人化をはかることに成功した。
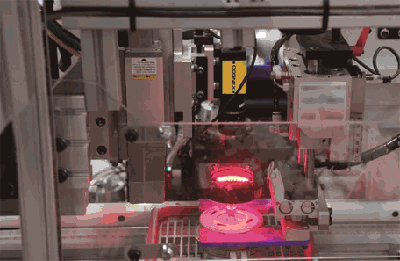
写真:AI技術による画像検査システムの工程
一方で、製造する石油ファンヒーターの機種ごとの形状の違いから、製造ラインを止めて90分かけて行っていたプレス機の金型交換や治具の取付け調整などの変更作業は、大型の設備投資をしない限り自動化が難しい。この作業の問題点を徹底的に洗い出し、並行作業や動線の改善などを行うことで大型の設備投資をすることなく大幅な時間短縮ができ、10分以内で出来るようになった。
これらの取組によって省力化された人材は、新たな製品の製造部門や組み立てラインなどで付加価値の高いレベルの業務に就けることができるようになった。
また、通常稼働の製造ラインとは別に「時短ライン」を設置して、子育て世代の社員が退職することなく、短時間勤務制度を活用して働きやすい会社づくりを進めている。
同社の海保雅裕取締役生産本部長は、「自動化などの合理化により、従業員にはより高度な仕事にチャレンジしてもらい、それに応じた収入を得られるようになれば従業員の人生がより豊かになると考えています。」と話す。(取材日:2019年11月14日)
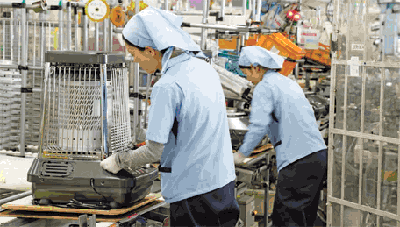
写真:暖房器具の時短ラインで短時間勤務する様子
株式会社ワールド山内(北海道北広島市)は1983年設立、最新の加工機械と自社開発した生産管理システムをインターネットで繋ぎ、すべての作業工程においてシステム化、マニュアル化を進めたことで、会社が持つ高い技術力により高品質で精密さが求められる航空宇宙産業や新幹線、自動車など幅広い分野の部品加工を強みとし、金属部品の3D設計開発や機械加工、溶接、組立、塗装などを一貫して手掛ける。同社では、超多品種少量生産、24時間自動運転で自動化・高効率化した生産体制を実現している。
同社工場の生産ラインは、部材の加工方法・手順や加工機械の稼働状況の管理など、すべての情報データの入力作業をなくすことで、作業の効率化・省力化を進めている。また作業者自身のムダな動きを工場内に設置した複数のWebカメラで捕捉し、リアルタイムの記録画像から「人の動きの見える化」を行うことで、作業者自身のムダな動きやトラブル対応時の振り返りが可能となった。
同社の人材育成に必要な社員研修マニュアルなどの教材は、工場内で加工する作業工程すべてを山内社長が分かり易くデジタル化して作成し、毎月開催して、新入社員のほか若手やベテラン社員問わず誰でも参加できるようにしている。講師は山内社長自ら行うほか、入社2~3年目の若手社員に行わせることで、自己の作業手順などを見直し、復習と併せて実践的なプレゼンテーション能力までを身に付けさせるようにしている。
同社のこういった先進的なデジタル化の取組によって、ものづくり現場では「今、誰がどんな作業を行い、製品の稼働状況がどうなっているか、今の今をリアルタイムに現状を知ることが本当のIoT。また数年前の過去のデータであっても、いつでも見られるのが自社の特徴であり、デジタル技術を活用した究極のトレーサビリティ(履歴管理)を開発し導入した。17年前にこの取組を始める前の工場内は、ベテラン技能者のカン・コツの技術に頼り、若手社員はその技術を見ながら習得していく、どこも当たり前のものづくり現場にあった光景を自らも肌で感じてきたからこその思いがあった。」と山内社長は話す。
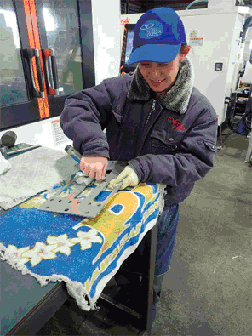
写真:切削機械加工後の仕上げの様子
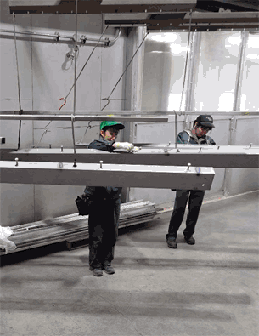
写真:塗装仕上げ工程の様子
今後は、WebカメラにAI機能を取り入れ、人やモノが正確に判別できるようになれば、作業段取り時間の短縮を図ることができるほか、遠隔地と本社工場とをインターネットで繋ぐことで、双方向でリアルタイムにやり取りしながら保守・メンテナンス作業の適切な指示や問題解決が出来るようになる。さらにデジタル化を進め、ロボットと作業者が共存できるようなものづくり現場にしたい考えだ。(取材日:2019年11月19日)
住友理工株式会社(愛知県小牧市)は、高機能ゴム、樹脂製品を主に製造し、自動車用防振ゴム・ホース部門は国内トップシェアを誇る。
同社は、愛知県小牧市に本社工場を構え、主力製品のマザー工場とし、グローバルに展開する各拠点の統括も行っている。
同社に特徴的なのが、生産ライン設備の故障による生産性低下を改善し、人のスキルや、カンコツに頼らない保全体制を築くためのIoTを活用した予知保全の取り組みである。この活動において推進の中核を担う「モノづくり革新センター」では主力製品ごとに、各事業部で8つのチームに分け、「生産革新」「ムダ取り」「IT活用」をキーワードに、モノづくり革新の実現を目指している。例えば、故障予知の取り組みでは、生産設備に振動や温度などを収集するセンサーを取り付け、収集した情報をモニターにリアルタイムで表示し、同時に本社工場のサーバーに蓄積していく。既に故障による設備停止時間は減少しているが、将来的には、このビッグデータとAIを活用し、さらに高精度な故障予知の仕組み構築を進めていくこととしている。
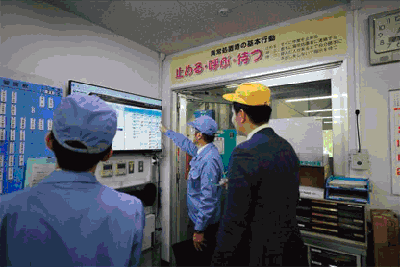
写真:故障予知のためのデータ蓄積
また、海外拠点で異常が発生した際には、IoTの仕組みによって得られた情報や、現地作業者が身に付けたカメラ映像を基に、本社工場の管理者が遠隔で指示や、助言を行える遠隔保全の取り組みも行っている。過去には、海外拠点で問題が起きるたびに、管理者が長時間かけて現地に出向いて対応を行っていたが、遠隔で指示ができるようになったことで渡航に要する時間や設備の停止時間を大幅に減少することができた。
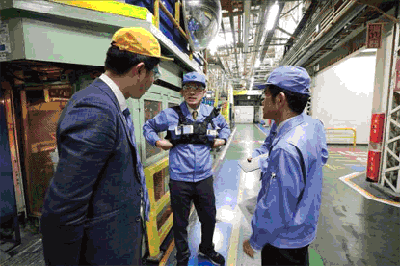
写真:胸に付けたカメラを活用して遠隔保全
また同社では、各部署から選抜された3~4名が約3ヶ月間職場を離れ、関連部門における事業課題をテーマに、工程の上長が指導員となって改善手法の指導を行う「F研」(フォアマン研修)注※が展開されている。昨年度末までの延べ受講者数は、4,698名を超え現場で自ら改善活動ができる人材を育成する歴史ある取り組みである。同社は現在、「グローバルF-ken」制度を海外拠点で展開しており、日本のモノづくりの強みと海外拠点の特徴を組み合わせて、改善活動の効果をより高めていくとしている。
注※ 監督者を目指す人のための研修
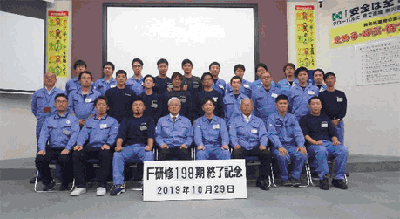
写真:1976年から続くF研
同社では、既に進みつつある自動車業界の大きな変革を見据え、あらゆる事業環境の変化に対応出来るよう、海外拠点も含め、デジタル技術を用いて現場の改善を実行できる人材づくりに取り組んでいくこととしている。(取材日:2019年11月27日)
株式会社山之内製作所(横浜市)は、1964年に創立。下請けの部品加工工場から始まった同社は、他社では難しい切削加工の技術を蓄積していくうちに、「困ったら山之内」と評判になった。現在同社はグループ2社(YSEC株式会社、JASPA株式会社)と協業し、得意とする精密加工技術を活かして航空機エンジンや人工衛星などの航空・宇宙機器、医療機器、通信機器をはじめとする精密部品の開発・製造を行っている。
同社におけるデジタル化の取組は、山内社長が約35年前から独学でIT技術を勉強しながら導入しており、「熟練技能者が持つ技術に頼りすぎるのはダメ。データ入力や繰り返し行う作業などは、コンピュータに行わせ、これからはクリエイティブな人材を育成していけるように」と山内社長は話す。
同社では多品種少量の部品製造が多いため、作るアイテムが違えば、そのたびに工具や治具などの取り換え作業が発生する。その作業の度に機械を停止して交換することは、手間もかかり、時間がもったいないと考え、製造部門にフレキシブル生産システム(FMS)を導入して、5軸マシニングセンタや縦型旋盤などの各種工作機械や三次元測定機・パレット交換などを材料治具自動交換ロボットと無人搬送システムで連携させた。受発注から製造ラインの稼働状況、機械トラブルや保全状況などを一元的に管理することで、パソコンやモバイル端末から、24時間リアルタイムな情報を共有できるようになった。こうしたデジタル化の取組によって、難しい加工技術やノウハウを蓄積した熟練技能者を、生産技術部門のクリエイティブ人材として、新規受注の部品製造に対応したものづくり工程を設計開発する部門に配置し活用した。さらに、作業手順を標準化したことから、作業者のカンやコツに頼ることによって発生していたヒューマンエラーを防ぎつつ、経験が浅い社員でも、複数の加工機械を操作して作業することができるようになり、以前は熟練技能を必要とした高付加価値、多品種少量の部品製造においても、若手や女性の活躍の場が大幅に広がった。
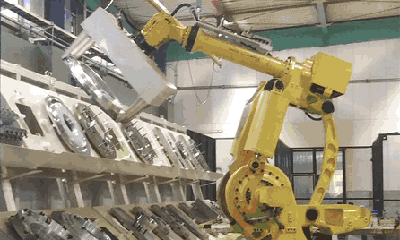
写真:全自動化された材料治具交換ロボット
同社製造ラインの中でも、きわめて高い品質が求められる航空機エンジンなどの重要部品の品質保証の分野は、デジタル化されたシステムだけで担うことは難しい。このため同社は、OEM認証や、さまざまな国際認証を取得する一方、製品表面や内部のごく微細な不連続などを調べる特殊な検査に関しては、国際認証を維持するだけでなく、世界有数の専門家を海外から招き、OJTなどによる人材育成、検査工程の仕組み改善を通じて、継続的な精度向上を図っている。
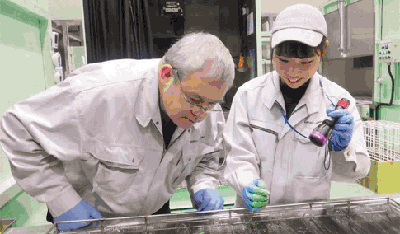
写真:品質検査技術のノウハウを海外技術者から指導を受けている様子
また、管理部門では、独自開発した社内生産管理システムやEDIシステムの導入など、各種の事務手続きにおいてもデジタル化したことで、受発注の管理や経理処理などのデータ入力作業や確認作業などが不要となった。各種作業マニュアルは社内システムに登録しておくことで、いつでも社員が自己学習可能な環境を構築し、社員教育にも活かしている。さらにビジネス版SNSをも活用し、情報連携、メンター制度や社員同士のコミュニケーション活性化のためのツール、社員の承認要求を満たす仕組みとしている。同社は、今後さらに生産性と、社員一人一人の仕事の付加価値をさらに高めていきたいとしている。(取材日:2019年11月13日)
(2)デジタル技術の活用を進めると同時に熟練技能の継承も進める好事例
ミシンを祖業に100年以上の歴史を持つブラザー工業株式会社は、主力製品のミシン、プリンターの製造に加え、産業機器分野では小型工作機械の製造を手掛ける。同社の産業機器は、主力商品である工業用ミシンのキーパーツを製造する工作機械を自社で制作するところから生まれた。1985年にCNCタッピングセンター第1号機を発売してから、すでに35年の歴史を持つ。現在では「30番」サイズの主軸径を持つコンパクトなマシニングセンタが、近年のスマートフォン部品需要増大を追い風に、市場での存在感を高めている。
工作機械の製造には、「部品加工」と「組立」の技能が必要となる。「部品加工」は、以前は職人が汎用機を使って手作業で行っていたが、NC機に置き換わったことで、若手が加工技能を身に着ける機会が無くなってきた。「組立」では、主力製品の全工程を一人で組める技能者が年々少なくなってきた。同社では、部品加工の原理原則と製品の全工程組立を基本から身に着けることを目的とした「匠道場」を2006年より開講している。製造に携わる中堅社員などを対象に、熟練技能を持った先輩が講師となって、「技能教育」と「認定試験」を行う。この取組で、継続的に技能伝承を行い、製造のエキスパート人材を育成する狙いがある。
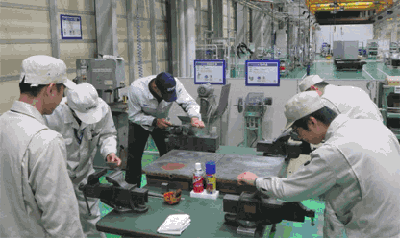
写真:デジタル屋台
また、工作機械ユニットの組立現場では、組付け作業をITで支援する(「デジタル屋台」と呼ばれる)仕組みを導入している。この装置では、作業指示がモニターに映し出され、その手順に応じてピッキングする部品や使用する工具が、格納された場所のランプが光って作業者に知らせる。また、ねじ締めに使用する工具にはトルクセンサーが組み込まれており、計測データから自動的に作業内容の合否を判断する。同社では、この仕組みを導入以降、作業手順間違いなどのヒューマンエラーが一切なくなり、さらに新人作業者の教育期間が、三分の一まで減少した。
組立ラインの検査には、従来紙のチェックシートを用いて品質チェックを行っていたが、現在ではタブレットを活用している。これによりタブレット導入前は、班長が工作機械1台の確認を行うのに10分要していたが、1分へと大幅に縮減され、さらにチェック漏れも全く無くなり、製品品質の向上を実現させた。同社では、デジタル技術を、ものづくり品質向上を目的に活用しているが、作業ミスによる手戻りが解消されるなど、労働生産性の向上に繋がっている。
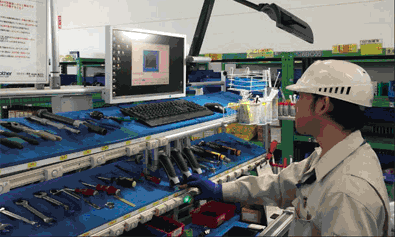
写真:「匠道場」での技能伝承の様子
また、女性の活用についても補助動力利用や治工具軽量化等により、無理なく作業ができるようにライン改善を進めている。作業者に占める女性割合は、2008年度が3%だったところ、2018年度には18%まで向上している。(取材日:2019年11月25日)
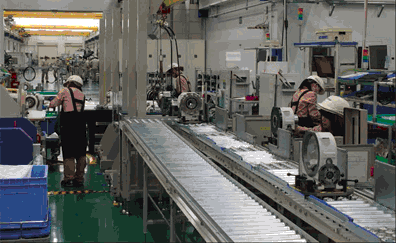
写真:活躍する女性
総合工作機械メーカーのオークマ株式会社(愛知県丹羽郡大口町)は、熟練の技とIoT、ビッグデータ、AI(人工知能)といった最新テクノロジーとを高度に融合させたものづくりを展開する。工作機械製造は、多種多様な顧客要求にきめ細かく対応するため、数千点から数万点にも及ぶ部品を加工・組み立てて製造する典型的な超多品種少量生産である。
同社では、2013年に複合加工機、中・大型旋盤、立形旋盤を生産する工場「Dream Site1」を建設し、生産設備の自動化・無人化と稼働状況の見える化に取り組んだ。続いて2017年には、自動化やスマート化の知見を活用し、ロボット活用による自動化領域をさらに拡大し、週末の72時間無人稼働を実現した工場「Dream Site2」を立ち上げた。「進捗・稼働状況監視システム」を含む工場コントローラの導入によりIoTを活用し工場の制御周期が高速化され、全体最適なカイゼンを促すことが可能となり、物流を含む生産進捗と設備稼働の一元的な分析、可視化を実現した。さらに2019年には、レーザ焼入れ機能を有する超複合加工機など工程集約をさらに推し進めた新工場「Dream Site3」を立ち上げた。
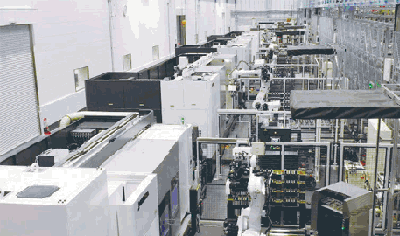
写真:「Dream Site」工場内の様子
自動化によって省人化された作業に従事していた人材は、付加価値の高い生産管理などの間接的な仕事に就くようになったという。工場内においては、フロア内に「見える化」を実現するモニターを設置し、管理者はタブレット端末で工程や機械の状況把握が可能である。ロボットや無人搬送車などを活用し、自動化を進めると、異常への対応が遅れる可能性も生まれる。そのため、IoT活用による監視を強化し、工場作業員のカバーできる範囲を広げることが重要となっている。多品種少量生産だからこそ、多様な顧客要求に対応し、効率的な作業方法を創造することが必要であり、この点は、「人間の仕事」であるとしている。
同社はデジタル化が進むものづくり現場を「熟練技能と自動化が織りなす夢の工場」とし、ものづくり人材の育成、技能伝承にも力を注ぐ。
1964年に始まった、社内の「技術・技能競技大会」は、入社10年未満の社員を中心に、「組立」「部品」「品質保証」「設計」「技術」「FA技術」「FA作業」「情報」「サービス」「営業」の10の部会に分けて技術を競い、部会ごとに認定・表彰することとしている。また、(国家)技能検定の取得も奨励しており、累計の有資格者は966人と、国内の企業では最多の実績を誇り、「現代の名工(※注釈)」が7名、「愛知の名工」が16名在籍する。工作機械の製造は熟練技能への依存度が高いため、高品質のものづくりを行うためには、このようにデジタル化のみならず熟練の技を融合させる仕組み作りが、新しい現場力構築の鍵となっている。
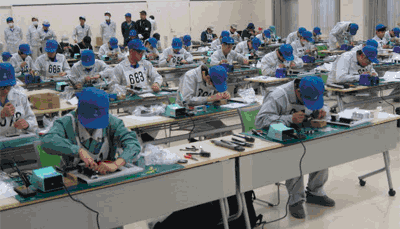
写真:技術・技能競技大会(FA作業部会)
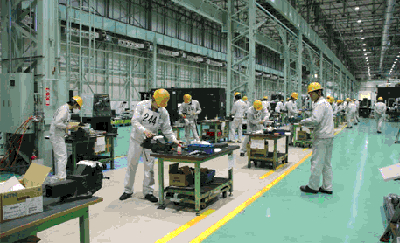
写真:技術・技能競技大会(組立部会)
同社では、今後、「Dream Site」で培った生産性革新のノウハウを「総合ものづくりサービス」としてユーザとも共有し、国内の製造業全体の生産性を高めることに貢献したいという狙いがある。(取材日:2019年11月26日)
独立行政法人造幣局(大阪府大阪市北区)は、1871年に明治新政府によって設立された。幕末の混乱期に乱れた貨幣制度を立て直し、列強に劣らない貨幣を造るため、当時としては最新の西洋式設備を導入し、貨幣の製造を開始した。
同局では、貨幣の製造、勲章・褒章及び金属工芸品等の製造などを行い、東京2020オリンピック・パラリンピック競技大会入賞メダルの製造も手掛ける。
貨幣材料の溶解から、貨幣の表裏の模様やギザの圧印・検査、計数・袋詰めに至るまで、多くの工程でデジタル化及び自動化が進んでいる。貨幣製造には偽造を防ぐ高度な技術が使われており、見る角度によって「500」の文字の中にさらに文字が見え隠れする「潜像」や、微細な線や点の加工技術のほか、斜めギザは特許取得の技術である。貨幣製造の最終工程では、この表裏の模様、縁にギザがある貨幣はギザも含めて、1分間に750枚というスピードで圧印され模様がつけられていく。その後、画像認識を用いて検査し、合格したものは袋詰めされた後封緘される。
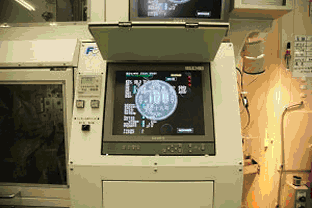
写真:デジタル化が進む貨幣工場
同局では、貨幣製造のデジタル化を進める一方で、国家または公共に対し功労のある方や、各分野で優れた行いのある方に授与される勲章、褒章の製造については、その工程の多くに手作業が含まれるため、熟練技能が必要となる。勲章の製造においては、NC彫刻機で部品を切り抜いた後は、やすりがけ、七宝の盛り付け・焼き付け、羽布での研磨、めっきに至るまで職人による手作業を行っている。
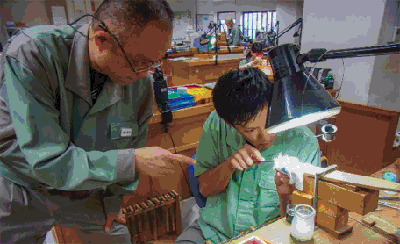
写真写真:やすりがけ指導の様子
職員の育成方針は、熟練職人によるOJTが中心であるが、熟練技能者のノウハウをまとめた、作業手順マニュアルを用いて指導を行う。マニュアルには実際の熟練技能者の作業を写した画像を多数使用し、作業室に備えられたPCでいつでも閲覧することが出来るようにしており、OJTと並行して活用されている。また、入局時からの経験年数に応じて、技能士検定に挑戦することを勧奨しており、資格取得者の氏名を廊下に掲示するなど職員の技能向上の意欲を高めることに積極的に取り組んでいる。現在延べ人数で、1級技能士21人、2級技能士23人が在籍している。さらに高い意欲を持った者には、芸術大学での工芸技能研修、老舗七宝店への派遣研修を行うなど、技術を高める機会も用意されている。
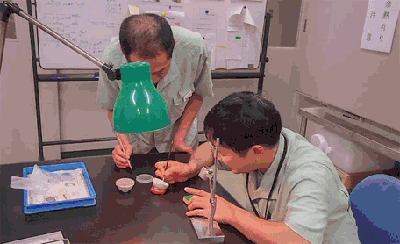
写真:七宝盛り付け指導の様子
「大勲位菊花章頸飾」に代表されるような希少な勲章の製造は、特に卓越した技能を持つ職人のみが携わる事が出来るため、職員の多くが、先に述べたようなOJTや、研修を活用しながら志高く、自らの技術を磨いている。(取材日:2019年10月28日)
(3)社内でデジタル技術の活用を担う人材を育成する好事例
日本ガイシ株式会社(愛知県名古屋市)は、特別高圧の送電線用のがいしや自動車排ガス浄化用セラミックス触媒担体、電子・電気機器や半導体製造装置に用いられるセラミックスなどを主力事業としている。2019年に創立100周年を迎え、更なる品質向上や多角化により中長期的な成長を目指しており、2018年度の連結売上高は過去最高を記録した。今後も全世界に裾野を広げ業績の拡大を目指すという。
同社の業績拡大を支えるのは、高い技術力と生産性であるが、成長の背景には「高度な分析力」がある。現在、生産拠点は国内外に数多く存在するが、それら拠点毎の生産性のばらつきを改善することが、更なる生産性向上の課題となっていた。
同社の製造技術本部内のグローバルエンジニアリングセンターでは、製造現場の設備から得られるビッグデータを分析し生産性や製造条件のばらつき原因を特定することで、生産性の最大化を目指している。
ビッグデータを活用した課題分析に着手したのは、10年ほど前である。取り組み前の当時、拠点における生産性の差が出ていることは把握できていたが、現場のオペレーターの動きや設備の使われ方を正しく把握できなかったため、課題の特定に至らず、オペレーターの「カンやコツ」頼みだったところがあった。そのため、担当者が足繁く製造現場に通い、設備の使われ方やオペレーターの動きを詳しく把握すると共に、設計部や情報システム部と連携して必要なデータを取得できる方法を構築した。
現在は設備に取り付けたセンサーやカメラで把握した情報を、各拠点だけでなく本社でも集約し、設備の稼働効率を総合的に判断する指標である設備総合効率(OEE)などを算出し生産性ばらつきや低下の原因が分析できる仕組みとなっている。その数値の見える化やそれを基に各拠点にフィードバックと改善活動支援を繰り返した結果、生産性が1年間で約10%上昇した工場もあった。今後は外部の有識者の助言も得ながらデータ活用の推進や更なるデータ分析力の高度化に取り組みたいという。
同社はこうした分析を行うためには、デジタル技術を使いこなし、さらに機能を改善していく能力をもったIT人材が必要であると考えている。全社の人材育成の方針は、社長をはじめとする経営層が出席する会議で審議決定する。各部門の課題と人材育成への要望を集約して現場の意見を反映させながら、必要な教育の適時適切な実施を行っており、人材育成に力を入れている。
また同社の国内外各拠点では様々な部門が横串で連携した「OEEフォーカスチーム」を結成し課題解決の方法を議論、共有するグローバル会議なども行っている。そうした場では、国内外の技術者、管理者同士が製造、生産計画、生産管理など様々な視点から議論を行い、労働生産性の向上策について共有する良い機会になっているという。
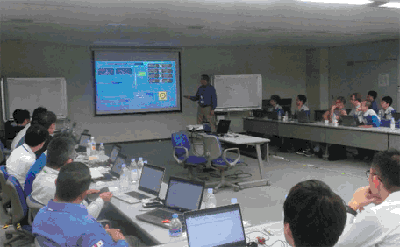
写真:工程担当者会議(OEE PEM)の様子
このように、デジタル分野をはじめとする技術を活用できる人材の確保と育成が同社の中長期的な成長のカギを握る。山田忠明常務執行役員人事部長は「技術を使いこなすだけでなく、技術を用いて新しいものを生み出す「発想力」をもった人材を数多く育てていきたい。」と今後の展望を語る。(取材日:2019年12月5日)
上田製袋株式会社(大阪府守口市)は昭和42年に「上田製袋工業所」として創業した製袋加工会社である。病院などの医療施設で感染防止のために減菌処理を行う際に使用する「滅菌バッグ」をはじめとするメディカル向けパッケージ(袋)の製造を主な事業としている。同社が製造する減菌バッグは、医療現場において対応できる衛生面、そして「密封されていること」と「開封しやすい」という、相反する性能を兼ね備えた性能が求められ、高度な技術と管理が必要となる。近年は、最新のレーザーを用いた樹脂フィルムの溶着の実用化に向けて、大学との共同研究も進めている。
同社では、年々高まる顧客からの品質向上と増産要請やベテラン人材の引退に伴う人材不足の状況を背景に、生産性向上を進めるため「稼働モニタリングシステム」の構築に向けた取組を進めている。IoTデバイスをシーリング機に取り付け、稼働状況を「見える化」する仕組みである。IoTデバイスは、数千円の市販マイコンボードに光センサーと無線発信機を組み合わせたもので、シンプルなIoTの取組である。
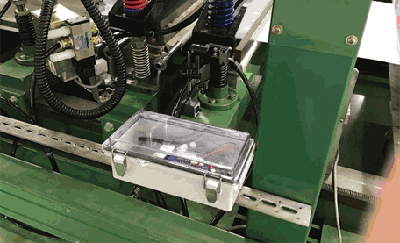
写真:機械に取り付けたセンサー
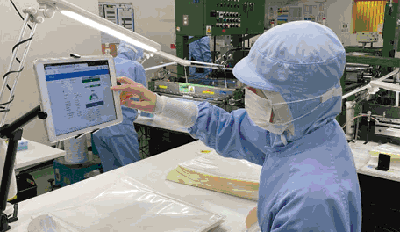
写真:作業状況をタブレットに入力する様子
これまでは、生産計画に基づいて進捗管理のみを行っていたが、「稼働モニタリングシステム」を導入して以来、機械トラブルや生産状況の稼働状況をリアルタイムで確認でき、トラブル時に管理者が即時対応可能となり、機械の稼働率向上につながった。また、集積したデータについては、社員の作業分析や人材教育の活用を目指している。
同社のデジタル化の取組が成功している理由として、社内で「IT推進委員会」を立ち上げた経緯が挙げられる。この委員会はシステム開発関連会社での業務経験のある上田社長をリーダーとし、デジタル機器の操作に抵抗の少ない若手社員により構成されており、社内のIoT活用に関する推進策や、デジタル化を進めるためのWebシステムの運営を企画している。この取組は、若手の自主性を促し、改善意識を高める人材育成の場ともなっている。
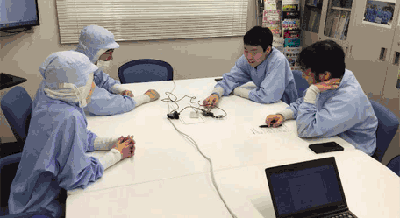
写真:IT推進委員会
上田社長は、中小企業のIoTの導入を成功させるためには、製造企業とIoTシステム開発会社の双方の技術を理解した「両者の間を埋める人材」が必要であると考える。「製造業のものづくり人材はデジタル技術に精通していないため、デジタル技術を活用した課題解決策を上手く表現できない。また、IoTシステムの開発会社は、製造業固有の業務に精通していないため、核心に迫る事が出来ずに、一般論でしか提案する事が出来ない。」という現状があるという。今後、同社では、社内の自動化・便利化をさらに進めることで業務効率化を図っていくこととしており、社員のITスキル向上のための勉強会のための時間を創出し、製造業とIT技術の両方を理解するハイブリッドな人材の育成を図ることで、さらなる生産性向上を行いたいとしている。(取材日:2019年10月29日)
大野ナイフ製作所は、刃物の町として700有余年の歴史を持つ岐阜県関市において、高級・高品質の包丁を製造する、創業103年の刃物メーカーである。同市では、刃物関連事業所の高齢化や、後継者不足が課題となっており、伝統的に分業制をとり大量生産を行っていた形態が成り立たなくなっていた。創業103年目となる同社では、20年前から90を超える包丁の製造工程全てを内製化することに取り組んできた。高品質を保ちながら量産するために、職人技を必要としない単純作業についてはロボットによる自動化を進めた。例えば、大まかな形を成形するベース加工などの単純作業をロボットに行わせることで、職人には刃先や柄の精密な研磨など、技術を必要とする一段上のレベルの仕事に注力できるようになり、品質の確保と生産性向上を両立することができた。
同社が製造する高級包丁は300種類程度あり、世界で販売されている。前述の通り高級包丁には多数の製造工程が必要であり、欠品によるビジネスチャンスを逃さないためには、市場での需要に合わせた製品の供給力が重要である。これを強化するために、段取り改善による生産効率化を図るとともに、変更があった際にすぐ作業内容を切り替えられる現場体制をつくる必要があり、IoTを活用した見える化を進めるきっかけとなった。
同社では大量にある生産工程を整理するために、40年ほど前から生産管理システムをオーダーメイドで外注し運用していたが、トップダウン方式で上手く浸透しなかったと大野社長は語る。そこで、3年前に3人の社員で「IoT推進チーム」を結成し、チームを中心に、社員全体で生産管理システムを構築に取り組むこととした。チームはまず、機械からオペレーションデータを収集し、工場内のモニターで工程の進捗をリアルタイムで確認できるように取り組んだ。さらに機械が停止した場合にはオペレーターが手首に着けた、ウェアラブル端末にチャットボットを用いて通知する仕組みも導入。これによりロボットの停止時間が削減され、オペレーターが作業の手を止め、稼働状況を確認する手間が無くなった。システムを作り上げるために、使いやすさにこだわって何度も現場社員と意見を交わし、画面に表示される色使いさえも調整を行ったことは特徴的である。
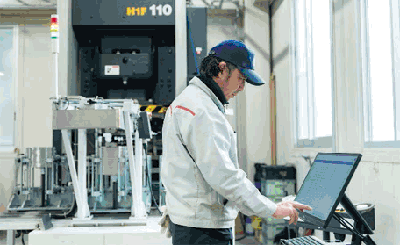
写真:ロボットと職人の共同作業
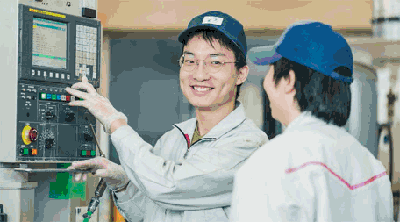
写真:CNCの教育風景
このように、大野社長直轄の下で風通しの良い環境で取り組んだほか、IoT推進チームの3名の社員には、積極的にIoT関連の見本市やセミナーに参加させ、最新の情報に触れさせるOJTの機会を用意した。多種多様なデジタル技術の、どれが自社に必要なものであるかを導き出すのは容易ではない。「職場を離れて知見を広める機会があったことが、革新性に繋がった」とチームメンバーは語っている。社員全員でつくった仕組みである事から、今回は抵抗なく現場に浸透し生産性の向上に寄与している。
同チームでは、IoTツールの導入だけでなく、RPAや電子ペーパーを導入して事務作業の簡素化にも取り組む。従来、事務社員が1時間かけてデータ入力していた作業が、RPA導入には5分で完了する事ができ、大幅に作業時間が削減された。
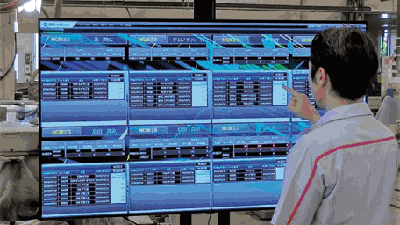
写真:実績収集と計画管理
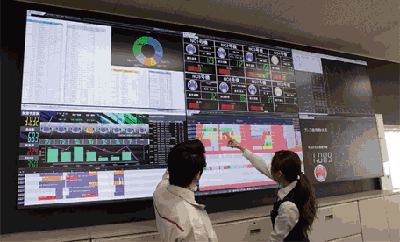
写真:進捗状況の「見える化」
同社では、デジタル化によって生まれた余力を活用して、カイゼン活動や、新たな事業領域の拡大、技能継承に向けた人材育成の時間を設けることができ、「絶え間ない革新的なものづくり」の展開に意気込む。(取材日:2019年11月27日)